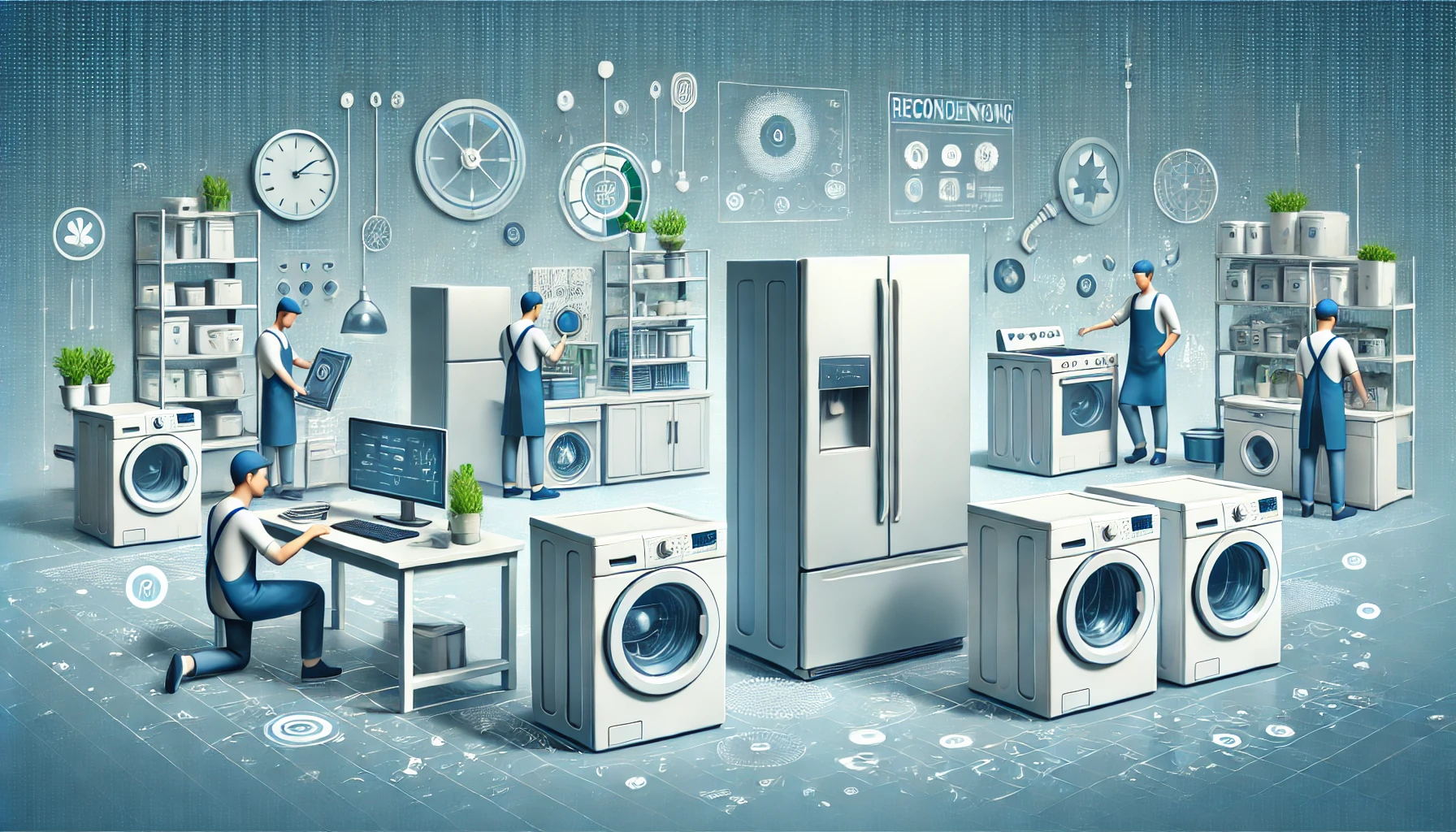
The refurbishment of household appliances is a booming sector that is gaining importance in our modern society.
Facing the rise of environmental concerns and the need to reduce electronic waste, the refurbishment market is positioning itself as a viable and sustainable solution.
The refurbishment process involves restoring used household appliances to a functional and sellable state, thus offering an economic and ecological alternative to buying new products.
The growing importance of refurbishment can be explained by several factors.
On the one hand, consumers are increasingly looking to reduce their ecological footprint by opting for refurbished products.
On the other hand, companies find in refurbishment an opportunity to generate additional revenue while contributing to environmental sustainability.
Indeed, the demand for affordable and quality household appliances continues to grow, and refurbishment provides a response to this demand while limiting the production of new appliances.
The aim of this article is to examine in depth the current state of the household appliance refurbishment market.
We will analyze statistics and trends, identify the main market players, and discuss the advantages and challenges of refurbishment.
We will also address software solutions that facilitate this process, with a particular focus on Refit, an innovative platform in this field, which we have developed.
The household appliance refurbishment market
Market Overview
The household appliance refurbishment market is booming.
With a growing awareness of economic and environmental benefits, more and more consumers and businesses are turning to this option.
Refurbished household appliances are refurbished, tested, and certified to guarantee their functionality and safety, thus offering a reliable and affordable alternative to new products.
Statistics and Trends
The growth of the household appliance refurbishment market is impressive.
In 2023, the sector saw a 15% increase compared to the previous year, and this trend is expected to continue in the coming years.
Consumers are increasingly turning to sustainable alternatives, thus promoting the rise of the refurbishment market.
Key figures reveal that more than 60% of household appliances sold as refurbished come from customer returns and unsold items from large stores.
This practice significantly reduces electronic waste while offering quality products at competitive prices.
Current trends also show a diversification of the types of refurbished appliances.
Once mainly focused on small appliances such as vacuum cleaners and coffee machines, the market is now expanding to large appliances such as refrigerators and washing machines.
This diversification responds to a growing consumer demand for more ecologically and economically friendly solutions.
Finally, online platforms specializing in the sale of refurbished products play a crucial role in market growth.
They offer increased visibility to refurbished products and facilitate consumers’ access to these alternatives.
Main Market Players
The household appliance refurbishment market is dominated by several large companies and innovative startups.
Among the market leaders, we find companies like Back Market and Recommerce, which specialize in selling refurbished products.
<!–
The challenges of refurbishment
Technical challenges
Refurbishing household appliances presents several technical challenges.
Common technical issues include the difficulty of finding compatible spare parts and the complexity of certain repairs. Modern household appliances increasingly integrate advanced technologies, making some technical interventions particularly complex.
Moreover, products from different brands may require specific skills and varied equipment to be properly refurbished.
To overcome these challenges, refurbishment companies are constantly innovating. They invest in training their technicians to handle a wide variety of products and technologies.
The use of specialized software also helps facilitate fault diagnosis and find appropriate solutions more quickly. Partnerships with appliance manufacturers can also play a crucial role in ensuring a steady supply of spare parts and technical information needed to carry out quality repairs.
Regulatory challenges
The refurbishment sector is also facing regulatory challenges.
Regulations and standards vary from country to country, and companies must ensure that their products comply with all applicable legal requirements.
This includes compliance with safety, energy efficiency, and environmental protection standards.
The impact of regulations on the refurbishment market can be significant. Companies often need to invest time and resources to stay informed of legislative changes and adapt their processes accordingly.
Compliance with standards can also lead to additional costs, particularly for compliance testing and certifications.
However, these challenges can also represent an opportunity for companies to differentiate themselves by guaranteeing the quality and safety of their products. By strictly adhering to standards, they can gain consumer trust and strengthen their reputation in the market.
Logistical challenges
Managing inventory and returns is another major challenge for refurbishment companies.
The logistics of transporting and storing refurbished appliances require meticulous organization to avoid losses and damages. Appliances must be carefully inspected, repaired, tested, and finally stored under appropriate conditions before being put back on the market.
Product returns, whether from dissatisfied customers or partnerships with retailers, must be effectively managed to minimize costs and maximize the chances of restoring the devices to working order. This requires efficient tracking and inventory management systems to ensure that each device is optimally processed.
Optimizing logistics also involves improving transportation processes. Reducing transport costs while ensuring the safety of devices is an ongoing challenge.
Companies can leverage technological advancements, such as logistics management software, to improve operational efficiency and reduce delivery times.
Software solutions for refurbishment
Refurbishment management software plays a crucial role in optimizing refurbishment processes.
They allow the automation and streamlining of various stages of refurbishment, from product reception to reconditioning and distribution. These tools offer better visibility and increased control over all operations, contributing to improving efficiency and profitability for refurbishment companies.
Main software on the market
Among the available software, Refit stands out for its ability to efficiently manage the entire refurbishment process.
Refit is designed to meet the specific needs of household appliance refurbishment companies.
It offers an integrated platform that enables tracking products at every stage, from reception to reconditioning, including quality control and distribution, as well as highly detailed refurbishment scenarios.
Key features of Refit
Refit offers several key features that facilitate the management of refurbishment operations.
Stock management is optimized through precise tracking of spare parts and finished products. The software also enables the monitoring of refurbished products, ensuring complete traceability from product entry to exit.
Process automation is another major advantage of Refit. The software automates repetitive and time-consuming tasks, freeing up time for technicians and improving overall efficiency.
Use cases
Several companies have already integrated Refit into their operations and are reaping significant benefits.
For instance, a large appliance refurbishment company reduced processing times by 30% thanks to process automation provided by Refit. Additionally, accurate inventory management helped cut costs associated with stock errors and material losses.
In summary, Refit proves to be an essential solution for household appliance refurbishment companies, offering advanced features to optimize every step of the process and improve profitability.
Use Cases
Several companies have already integrated Refit into their operations and are reaping significant benefits.
They have observed a noticeable improvement in efficiency and a reduction in processing times.
Moreover, Refit is present in dozens of warehouses across France, demonstrating its robustness and ability to meet the varied needs of businesses of all sizes.
Refit stands out as an essential solution for appliance refurbishment companies, offering advanced features to optimize each step of the process and improve profitability.
Focus on Refit
Introduction to Refit
Refit is an innovative solution dedicated to appliance refurbishment.
Designed to meet the specific needs of refurbishment businesses, Refit offers an integrated platform that simplifies and optimizes the entire process, from product reception to restoration and distribution.
Refit’s services include inventory management, product tracking, and task automation, enabling companies to enhance efficiency and profitability. The platform is intuitive and easy to use, facilitating its adoption by technical and logistics teams.
Refit stands out for its ability to adapt to different types of appliances, offering a flexible and robust solution for businesses of all sizes. The platform is already used by several renowned companies in the sector, confirming its effectiveness and reliability.
Features and Benefits of Refit
Refit offers several key features that facilitate refurbishment chain management.
Inventory management is optimized through precise tracking of spare parts and finished products. Companies can thus monitor their inventory in real-time and anticipate procurement needs.
Process automation is another major advantage of Refit. The software automates repetitive and time-consuming tasks, such as product sorting, functionality testing, and repair tracking. This frees up time for technicians to focus on higher-value tasks.
Refit also integrates quality control tools that ensure each refurbished product meets safety and performance standards before being marketed.
Process optimization through Refit results in reduced operational costs and improved customer satisfaction. Companies can offer high-quality refurbished products while minimizing returns and complaints.
Customized end-to-end refurbishment scenarios are a standout feature.
User Feedback
Refit has received very positive reviews from its users.
Companies like Decathlon and Reconomia have adopted Refit to manage their refurbishment operations and validated its utility.
Case studies show that companies using Refit have been able to increase productivity while reducing operational costs.
Customers particularly appreciate Refit’s ability to integrate with other existing management systems via API, making the transition to a more automated and efficient solution easier.
How to Use Refit for Your Business
Using Refit for your business is simple and intuitive.
The platform is designed to be easily integrated with your existing systems, thus minimizing disruptions during the transition.
To start using Refit: you can visit this page for more information.
Sources:
Market Watch – Refurbishment 2023
Statista – Growth of Refurbished Market
Green Alliance – Circular Economy Report
Consumer Reports – Refurbished Appliances
Back Market – About Us
Recommerce – Company Overview
GreenWEEE – Innovation in Refurbishment