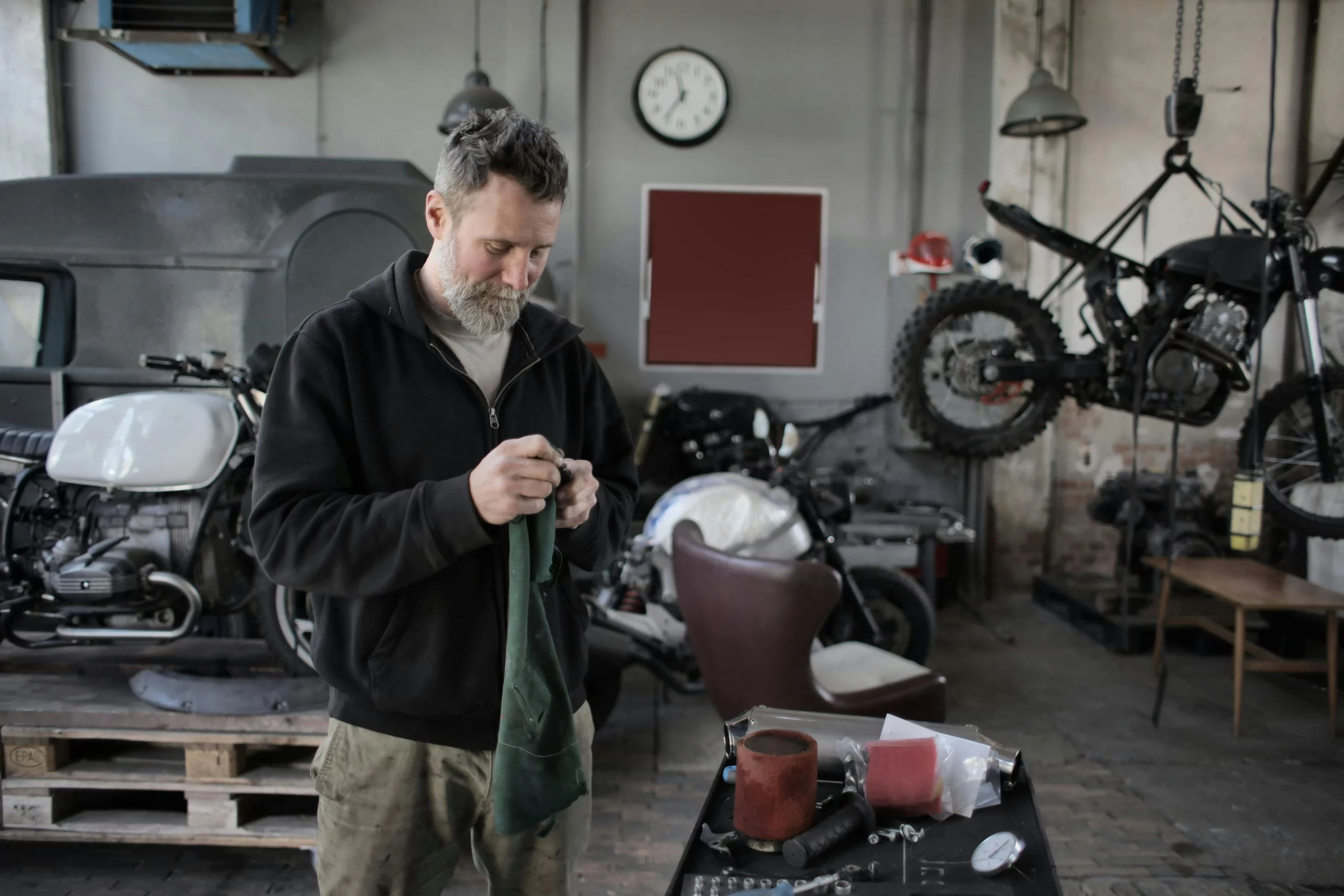
Maîtriser les coûts du reconditionnement en 2025
En 2025, le reconditionnement occupe une place centrale dans l’économie circulaire. Selon une étude de Statista, le marché mondial des produits reconditionnés pourrait dépasser 80 milliards d’euros d’ici la fin de la décennie. Cette croissance exponentielle s’explique par une double exigence.
D’une part, les consommateurs recherchent des alternatives plus abordables tout en réduisant leur impact environnemental. D’autre part, les entreprises doivent impérativement trouver des solutions pour optimiser leurs coûts de reconditionnement, sous peine de voir leur rentabilité fragilisée par des dépenses mal maîtrisées.
Un secteur en pleine mutation qui impose de nouveaux défis
Face à cette expansion rapide, les entreprises doivent relever plusieurs défis stratégiques. D’abord, elles doivent rationaliser leurs coûts de reconditionnement malgré l’augmentation du volume de retours et la diversité des références produits. Ensuite, elles doivent apprendre à gérer plusieurs sites et équipes répartis sur différents territoires, ce qui complexifie la coordination des opérations.
Par ailleurs, les réglementations environnementales deviennent de plus en plus strictes. Elles imposent notamment une traçabilité renforcée et une meilleure gestion des déchets, obligeant ainsi les entreprises à revoir leurs pratiques. Dans ce contexte, la digitalisation et l’automatisation des processus apparaissent comme des leviers incontournables.
Les solutions SaaS, à l’image de Refit, permettent aujourd’hui d’optimiser l’ensemble du processus en réduisant les pertes, en améliorant la traçabilité et en garantissant une qualité homogène des produits reconditionnés. Cependant, au-delà de l’aspect technologique, la maîtrise des coûts de reconditionnement passe aussi par une optimisation des flux logistiques et une organisation plus fluide des opérations.
Ce dossier met en lumière les stratégies à adopter pour limiter les dépenses tout en renforçant la productivité et la qualité des produits remis sur le marché.
Les principaux défis pour optimiser les coûts du reconditionnement
Le reconditionnement repose sur plusieurs étapes incontournables : diagnostic, réparation, remplacement de pièces, tests de contrôle et mise en circulation du produit final. Lorsqu’elles ne sont pas parfaitement maîtrisées, ces phases peuvent entraîner des coûts excessifs, nuisant ainsi à la rentabilité globale de l’entreprise.
L’un des premiers obstacles concerne la fragmentation des opérations. À mesure que les références produits se multiplient, chaque catégorie peut nécessiter des composants spécifiques, des procédures adaptées et des délais variables. D’après une étude menée par Deloitte en 2022, 65 % des entreprises du e-commerce ont observé une augmentation des retours ces dernières années. Sans une gestion rigoureuse, ces flux deviennent difficiles à anticiper, générant ainsi des surcoûts en matière de stockage, de transport et de manutention.
En parallèle, les attentes des consommateurs évoluent rapidement. Désormais, ils ne se contentent plus d’acheter un produit reconditionné uniquement pour des raisons économiques. Ils exigent une qualité comparable au neuf, tout en restant attentifs aux engagements environnementaux des entreprises. Cette exigence impose donc des contrôles qualité plus stricts, ce qui peut rallonger les délais et augmenter les coûts opérationnels, notamment pour les entreprises multi-sites.
La pression réglementaire s’intensifie également. En Europe, la Commission européenne a fixé des objectifs ambitieux, visant à augmenter de 20 % le recyclage des composants électroniques d’ici 2026. Pour se conformer à ces exigences, les entreprises doivent investir dans des outils de traçabilité plus performants et revoir leur gestion des déchets, ce qui représente un coût supplémentaire.
Enfin, la gestion des opérations multi-sites constitue un véritable casse-tête. Coordonner plusieurs entrepôts sans outil centralisé entraîne bien souvent des erreurs : doublons d’achats, approvisionnements mal calibrés ou encore surcoûts logistiques. Afin d’éviter ces dérives, il est essentiel de standardiser les procédures, d’automatiser le suivi des stocks et d’analyser en temps réel la performance de chaque site.
Dans les sections suivantes, nous verrons comment identifier et réduire ces coûts cachés, tout en optimisant les dépenses sur le long terme.
Les coûts cachés du reconditionnement et leurs impacts
Bien souvent sous-estimés, les coûts cachés représentent une part non négligeable des pertes financières liées au reconditionnement. Selon l’Institut de la Logistique Française (2023), ces frais invisibles peuvent peser jusqu’à 15 % des dépenses globales.
L’un des premiers postes de coût concerne la mauvaise gestion des flux logistiques. Lorsqu’une entreprise ne maîtrise pas parfaitement ses approvisionnements, elle risque rapidement de se retrouver avec un excédent ou une pénurie de pièces détachées, ce qui entraîne des retards de production et des coûts de stockage inutiles.
Par ailleurs, les erreurs humaines peuvent alourdir la facture. Un simple mauvais étiquetage ou une sélection incorrecte de pièces ralentit la chaîne de production et augmente le risque de non-conformité. D’après McKinsey (2021), une réduction de 10 % des erreurs humaines dans la supply chain permettrait d’améliorer la marge opérationnelle de 2 à 3 %.
À cela s’ajoutent les retards logistiques, souvent synonymes de dépenses additionnelles. Lorsque les délais ne sont pas anticipés, l’entreprise doit supporter des coûts supplémentaires : frais de transport express, stockage prolongé des produits en attente ou encore pénalités contractuelles imposées par certains clients.
Pour limiter ces pertes financières, il est primordial d’optimiser le suivi des opérations. L’automatisation du suivi des stocks, l’utilisation d’alertes en cas d’anomalie et l’exploitation de logiciels d’analyse prédictive permettent d’anticiper les fluctuations de la demande et d’ajuster les flux en conséquence.
Des consommateurs plus exigeants et une réglementation plus stricte
Le marché du reconditionné a longtemps été considéré comme une alternative au neuf, surtout pour les consommateurs soucieux de réaliser des économies. Cependant, cette perception a évolué. Aujourd’hui, les acheteurs attendent des produits de qualité équivalente, tout en veillant à leur impact environnemental.
Ils recherchent des garanties sur plusieurs points essentiels :
- Une fiabilité irréprochable : un produit reconditionné ne doit pas être synonyme de compromis sur la performance ou l’esthétique.
- Un prix attractif : il doit rester plus avantageux que le neuf tout en justifiant sa valeur.
- Une transparence environnementale : les consommateurs veulent connaître l’empreinte carbone associée au processus de reconditionnement.
Dans le même temps, les réglementations se renforcent. La loi AGEC (anti-gaspillage pour une économie circulaire) en France, ainsi que les directives européennes favorisant la réparation et la réutilisation des produits, imposent aux entreprises d’intégrer ces préoccupations dans leur modèle économique.
Ainsi, celles qui s’appuient sur des solutions durables et des stratégies circulaires parviennent non seulement à réduire leurs coûts, mais aussi à renforcer leur image de marque. En misant sur une traçabilité exemplaire et une gestion rigoureuse des flux, elles transforment une contrainte en un véritable avantage concurrentiel.
Maîtriser les coûts du reconditionnement ne se résume donc pas à réduire les dépenses. Il s’agit aussi d’adopter une approche stratégique qui favorise la durabilité, l’optimisation des ressources et la transparence vis-à-vis des consommateurs.
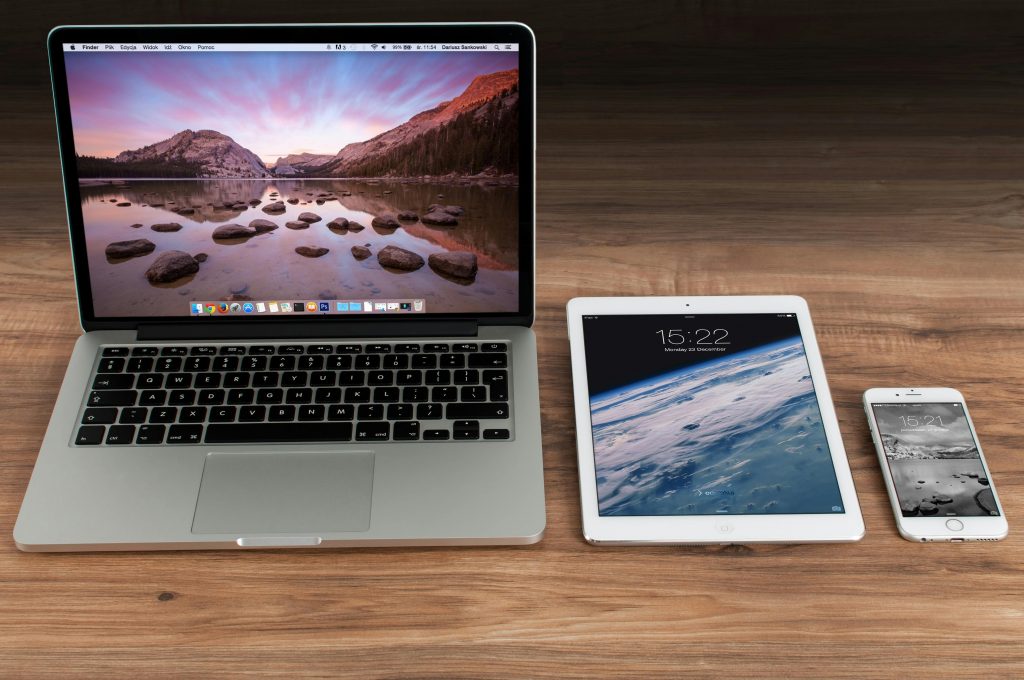
L’impact des solutions digitales comme Refit sur la maîtrise des coûts
Face aux nombreux défis du reconditionnement, les solutions digitales apportent une réponse stratégique.
Selon Gartner, les entreprises qui intègrent des plateformes de gestion automatisée dans leur supply chain pourraient réduire leurs coûts du reconditionnement de 15 % à 25 % sur cinq ans.
Un logiciel spécialisé, comme Refit, permet d’optimiser plusieurs aspects du reconditionnement pour gagner en efficacité et en rentabilité.
Standardisation des procédures pour une meilleure fluidité
Dans un environnement où chaque produit peut nécessiter un traitement spécifique, structurer les processus devient essentiel.
Avec un outil comme Refit, chaque référence suit un scénario prédéfini, de l’étape de diagnostic à la re-commercialisation. Cette approche standardisée réduit les écarts de traitement et facilite la circulation des informations entre les équipes.
Grâce à cette organisation, les délais de reconditionnement sont mieux maîtrisés, ce qui limite les surcoûts liés aux erreurs humaines et aux retards.
Automatisation des tâches répétitives pour une productivité accrue
Le reconditionnement repose encore sur de nombreuses tâches manuelles qui ralentissent les opérations et augmentent les risques d’erreur.
Avec l’automatisation, certaines actions chronophages comme l’étiquetage, la génération de bons de réparation ou encore le suivi des étapes sont prises en charge par le logiciel.
Ce gain de temps permet aux équipes de se concentrer sur des tâches à plus forte valeur ajoutée, tout en réduisant les erreurs de saisie et les doublons.
Une analyse des données en temps réel pour ajuster la stratégie
Les entreprises qui maîtrisent leurs coûts du reconditionnement ont un point commun : elles exploitent leurs données pour prendre de meilleures décisions.
Grâce aux tableaux de bord analytiques, les responsables peuvent suivre des indicateurs clés tels que :
- Le taux de réussite des tests qualité
- Le nombre de pièces utilisées par produit
- Le temps moyen consacré à chaque étape du processus
Avec ces informations en temps réel, il devient possible d’identifier immédiatement les inefficacités et d’ajuster les ressources en conséquence.
Une traçabilité complète pour garantir la conformité et la confiance
La traçabilité est devenue un enjeu majeur, tant pour les normes environnementales que pour la satisfaction client.
Chaque produit reconditionné doit être suivi à chaque étape : de son entrée dans l’atelier à sa remise sur le marché.
Avec une solution digitale, tout est documenté et centralisé, ce qui permet de répondre aux exigences réglementaires et d’assurer une transparence totale sur l’origine et l’état du produit.
En plus d’être un levier de conformité, cette traçabilité renforce la confiance des consommateurs et partenaires commerciaux, qui sont de plus en plus attentifs aux engagements des entreprises en matière d’économie circulaire.
Grâce à ces outils, la gestion d’un reconditionnement multi-sites devient plus fluide. Les stocks sont mis à jour en temps réel, réduisant ainsi les risques de rupture ou d’excédents.
Capgemini Research Institute estime d’ailleurs que les entreprises qui exploitent pleinement ces solutions sont deux fois plus susceptibles d’atteindre une marge opérationnelle supérieure à 10%.
Automatisation et optimisation des flux de reconditionnement
L’automatisation est un levier clé pour limiter les pertes et optimiser la rentabilité du reconditionnement.
Selon PwC, 45 % des entreprises industrielles considèrent que les tâches répétitives consomment trop de temps et d’énergie.
Dans le secteur du reconditionnement, ces tâches sont nombreuses : saisie manuelle des données, impression des étiquettes, vérification des stocks… Autant d’étapes qui peuvent être optimisées avec des solutions adaptées.
Répartition intelligente des tâches et suivi en temps réel
Une plateforme comme Refit permet de configurer des workflows intelligents pour mieux gérer les ressources disponibles.
Dès qu’un produit entre en reconditionnement, il est automatiquement attribué à l’équipe la plus adaptée, en fonction de la charge de travail et des compétences requises.
Ce suivi en temps réel évite les goulets d’étranglement et permet d’ajuster la cadence en fonction des volumes entrants.
Des alertes pour anticiper les problèmes
Dans une chaîne de production classique, les retards sont souvent détectés trop tard, ce qui génère des coûts supplémentaires en logistique et en main-d’œuvre.
Avec un système d’alerte intégré, toute anomalie est signalée immédiatement :
- Une pièce en rupture de stock
- Un retard sur une commande
- Une non-conformité détectée lors des tests
Ces notifications permettent aux managers d’intervenir rapidement et d’optimiser la gestion des stocks et des plannings.
Digitalisation des documents et suppression du papier
Le recours à des documents physiques entraîne souvent des erreurs, des pertes d’informations et des lenteurs administratives.
Dématérialiser les fiches techniques, les bons de réparation et les certificats de conformité offre plusieurs avantages :
- Un accès simplifié aux informations, même à distance
- Une réduction du risque d’erreurs et de doublons
- Une meilleure traçabilité des interventions
En réduisant le temps consacré aux tâches administratives, les équipes peuvent se concentrer sur le cœur du métier : le reconditionnement et l’amélioration continue des processus.
L’ensemble de ces optimisations permet d’améliorer significativement la rentabilité et de maîtriser les coûts du reconditionnement sur le long terme.
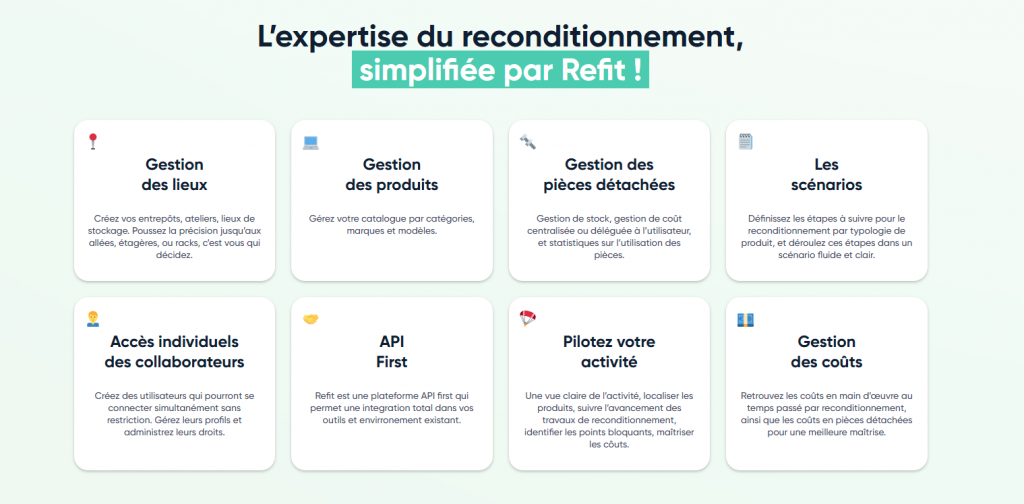
Traçabilité et réduction des pertes
La traçabilité est un élément central de la performance opérationnelle. En connaissant l’historique détaillé d’un produit – de son origine aux interventions techniques subies – il devient plus facile de garantir une qualité optimale et de limiter le gaspillage.
Grâce à des outils comme Refit, chaque article dispose d’une fiche digitale recensant toutes les actions effectuées. Depuis la réception initiale jusqu’à la remise en stock, toutes les étapes sont consignées de manière transparente.
Cette visibilité apporte plusieurs avantages. D’une part, elle réduit les pertes liées aux erreurs de réaffectation ou aux écarts d’inventaire. D’autre part, elle permet de calculer avec précision les coûts de main-d’œuvre et de pièces pour chaque intervention. Enfin, elle aide à détecter les sources de gaspillage, qu’il s’agisse d’un taux de retour anormalement élevé ou d’interventions redondantes sur un même type de produit.
Les tableaux de bord automatisés facilitent encore cette optimisation. En analysant les tendances, ils alertent sur les anomalies – comme un taux d’échec inhabituel sur un site ou des délais de réparation excessifs – et suggèrent des actions correctives. Selon l’European Logistics Association (2023), un suivi numérique permettrait de réduire jusqu’à 30 % les pertes de stock par rapport aux méthodes manuelles.
Étapes clés pour optimiser le reconditionnement en 2025
Avec la montée en puissance du marché du reconditionné, les entreprises doivent structurer leurs processus pour maintenir leur compétitivité. Pour cela, trois piliers s’imposent : la digitalisation, la maîtrise des coûts et l’intégration d’une approche durable.
Digitaliser les processus avec un logiciel SaaS
La digitalisation est un levier incontournable pour améliorer l’agilité et la réactivité des opérations. Un logiciel SaaS comme Refit offre une plateforme centralisée, accessible à tous les intervenants : techniciens, managers et partenaires.
Grâce à ce type d’outil, les documents dispersés et les tableurs obsolètes appartiennent au passé. Chaque étape du processus – test, validation, changement de pièce – est enregistrée et consultable en temps réel dans un système unique.
Ce mode de fonctionnement présente plusieurs avantages :
- Moins d’erreurs de saisie et une meilleure communication entre les équipes.
- Réaffectation plus rapide des ressources en cas d’imprévu.
- Optimisation des plannings grâce à une vision en temps réel.
Pour les entreprises multi-sites, l’impact est encore plus significatif. Grâce à une synchronisation instantanée des stocks et des interventions, les décisions peuvent être prises rapidement, en fonction des besoins et des disponibilités.
Réduire les coûts tout en augmentant la qualité
Optimiser les coûts ne signifie pas sacrifier la qualité. Au contraire, les entreprises qui réussissent dans le reconditionnement sont celles qui investissent dans des outils d’analyse pour identifier précisément les inefficacités.
En comparant les marges par catégorie de produit, il devient plus facile de déterminer quels articles sont les plus rentables et où concentrer les efforts d’optimisation. De même, l’analyse des flux de travail permet d’identifier les goulots d’étranglement et d’ajuster les process en conséquence.
Un autre levier d’amélioration réside dans l’écoute des retours clients. Suivre les problèmes récurrents permet de perfectionner les protocoles de test et d’anticiper certaines pannes.
Les solutions comme Refit jouent un rôle clé en fournissant un pilotage précis des coûts à chaque étape du reconditionnement. Avec une visibilité en temps réel, il devient possible de savoir où se situent les principales dépenses et comment améliorer la rentabilité globale.
En parallèle, cette approche permet d’améliorer encore la qualité des produits remis sur le marché. Lorsqu’une anomalie est détectée, les équipes peuvent intervenir immédiatement et éviter que le problème ne se reproduise sur d’autres articles.
Intégrer une stratégie durable et circulaire
Le reconditionnement ne se limite pas à la réduction des coûts. Il s’inscrit également dans une logique d’économie circulaire, visant à prolonger la durée de vie des produits et à minimiser l’empreinte environnementale.
Pour aller plus loin, certaines pratiques doivent être mises en place :
- Assurer une traçabilité complète des composants, afin de favoriser leur réutilisation ou leur recyclage.
- Optimiser la gestion des déchets, en mettant en place des processus de tri sélectif et de valorisation des matériaux.
- Intégrer des indicateurs environnementaux pour répondre aux normes et aux attentes croissantes des consommateurs.
Un logiciel SaaS facilite cette démarche en offrant un suivi détaillé des matières premières utilisées. Certaines solutions intègrent même des modules de reporting environnemental, permettant d’analyser l’impact écologique du processus de reconditionnement.
En adoptant ces bonnes pratiques, les entreprises ne se contentent pas de réduire leurs coûts. Elles gagnent aussi en crédibilité sur le marché, en affichant un engagement clair en faveur de la durabilité et de l’innovation.x et une intégration possible avec des modules de reporting environnemental. Les entreprises gagnent alors en visibilité sur les volumes de déchets évités et peuvent ainsi valoriser leurs efforts de durabilité auprès de leurs partenaires et de leur clientèle.
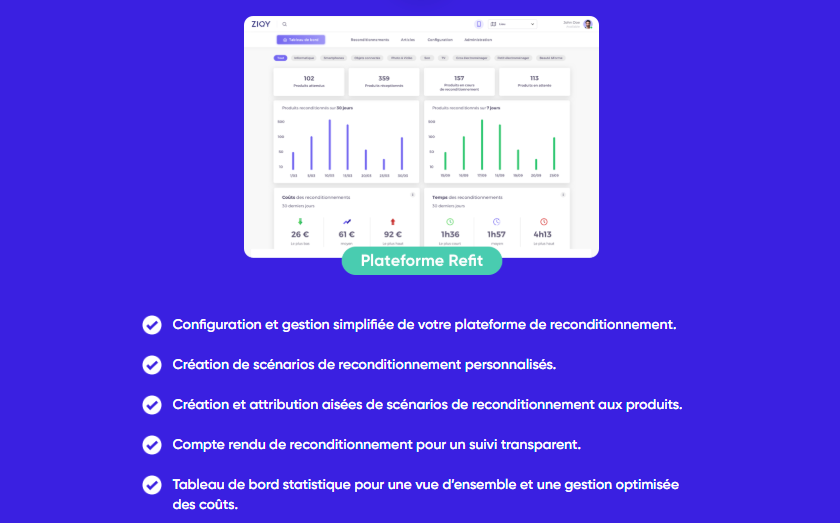
Les avantages mesurables des solutions digitales comme Refit
Loin d’être un simple gadget, une plateforme spécialisée dans le reconditionnement offre des avantages concrets et quantifiables. En effet, elle permet non seulement d’optimiser les coûts, mais aussi d’améliorer la rentabilité et la productivité. Ainsi, les entreprises qui adoptent ces solutions gagnent en efficacité et en compétitivité.
Réduction des coûts directs et indirects
Grâce à l’automatisation et à la standardisation des tâches, les coûts directs – comme la main-d’œuvre et les pièces détachées – diminuent considérablement. En parallèle, les coûts indirects, liés aux erreurs, aux retards et aux surplus de stock, sont également réduits.
Selon une enquête menée par l’AFIL (Association Française de l’Industrie Logistique) en 2022, l’adoption d’un outil centralisé peut faire baisser jusqu’à 30 % les dépenses associées aux erreurs d’aiguillage ou aux commandes de pièces inutiles. Par conséquent, les entreprises qui digitalisent leur gestion limitent les pertes financières tout en améliorant leur réactivité.
De plus, en unifiant toutes les données au sein d’un même système, elles éviten la double saisie et réduisent les risques de défaillance. Cela signifie que les équipes disposent d’une base de travail fiable et cohérente. Grâce à cette consolidation des informations, il devient également plus facile de négocier des tarifs avantageux avec les fournisseurs et les transporteurs, ce qui renforce encore la maîtrise des coûts.
Augmentation de la rentabilité et de la productivité
Pour être réellement rentable, une chaîne de reconditionnement doit fonctionner avec rapidité et précision. Autrement dit, chaque étape doit être optimisée afin de minimiser les pertes et d’accélérer les cycles de production.
Grâce aux reportings en temps réel, les responsables ont accès à des indicateurs clés (KPI) leur permettant d’ajuster leurs stratégies instantanément. Par exemple, ils peuvent identifier les goulets d’étranglement, réaffecter les ressources en fonction des priorités et anticiper les problèmes avant qu’ils ne surviennent.
D’après une étude de Bain & Company (2023), les entreprises qui s’appuient sur un système d’information bien paramétré peuvent améliorer leur productivité de 25 %. Pourquoi ? Parce que la réduction des tâches répétitives libère du temps pour les opérations à plus forte valeur ajoutée.
En conséquence, cette efficacité accrue ne se traduit pas seulement par une meilleure gestion des flux. Elle permet également aux entreprises d’innover, de développer de nouveaux marchés et d’améliorer l’expérience client. Ainsi, en gagnant du temps et en limitant les erreurs, elles peuvent consacrer davantage de ressources à l’expansion de leur activité.
Pourquoi Refit est essentiel pour le reconditionnement en 2025
Le reconditionnement devient de plus en plus complexe, notamment en raison de la hausse des retours, de la gestion des opérations multi-sites et des exigences environnementales croissantes. Face à ces défis, les entreprises doivent absolument franchir le cap de la digitalisation si elles veulent gagner en rentabilité.
D’une part, la maîtrise du reconditionnement repose sur un pilotage précis. D’autre part, ce pilotage ne peut être efficace qu’avec des outils offrant une visibilité continue sur les stocks, la main-d’œuvre et l’état des produits.
Dans ce contexte, Refit s’impose comme une solution incontournable. Grâce à sa plateforme dédiée, il fluidifie chaque étape du processus, de la réception des articles jusqu’à leur remise sur le marché. En outre, il assure une traçabilité complète, garantissant ainsi une gestion transparente et efficace.
Aujourd’hui, la concurrence ne se limite plus au seul facteur prix. Désormais, d’autres critères entrent en jeu :
- La qualité du reconditionnement, qui doit être irréprochable.
- La responsabilité sociale et environnementale, qui devient un argument de poids.
- La rapidité de mise sur le marché, qui influence directement les marges.
Comme le démontrent les études citées, l’adoption d’une solution digitale comme Refit constitue un véritable levier de transformation. Finalement, la différence entre un reconditionnement coûteux et une activité pérenne repose largement sur la capacité des entreprises à optimiser leurs processus.
En intégrant ces nouvelles technologies, elles s’assurent un avantage concurrentiel durable et maximisent leurs performances à long terme.
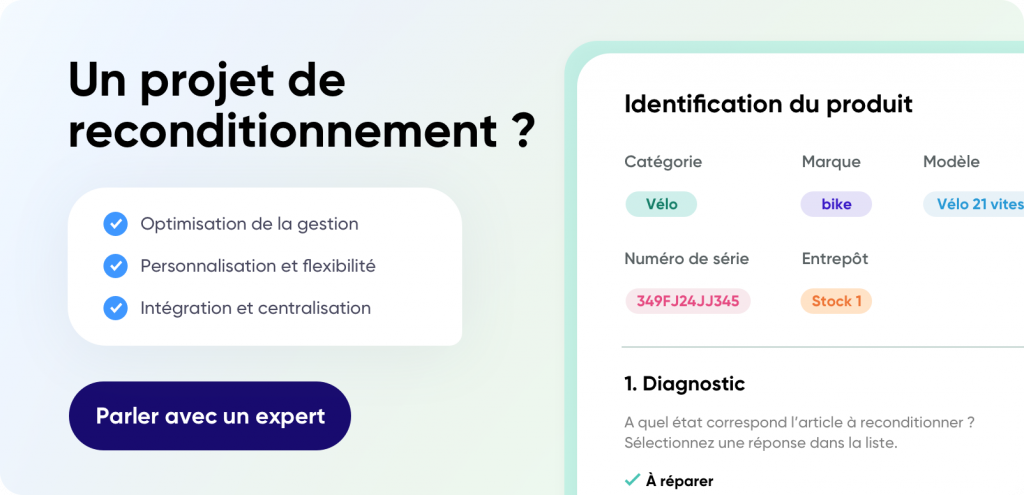